
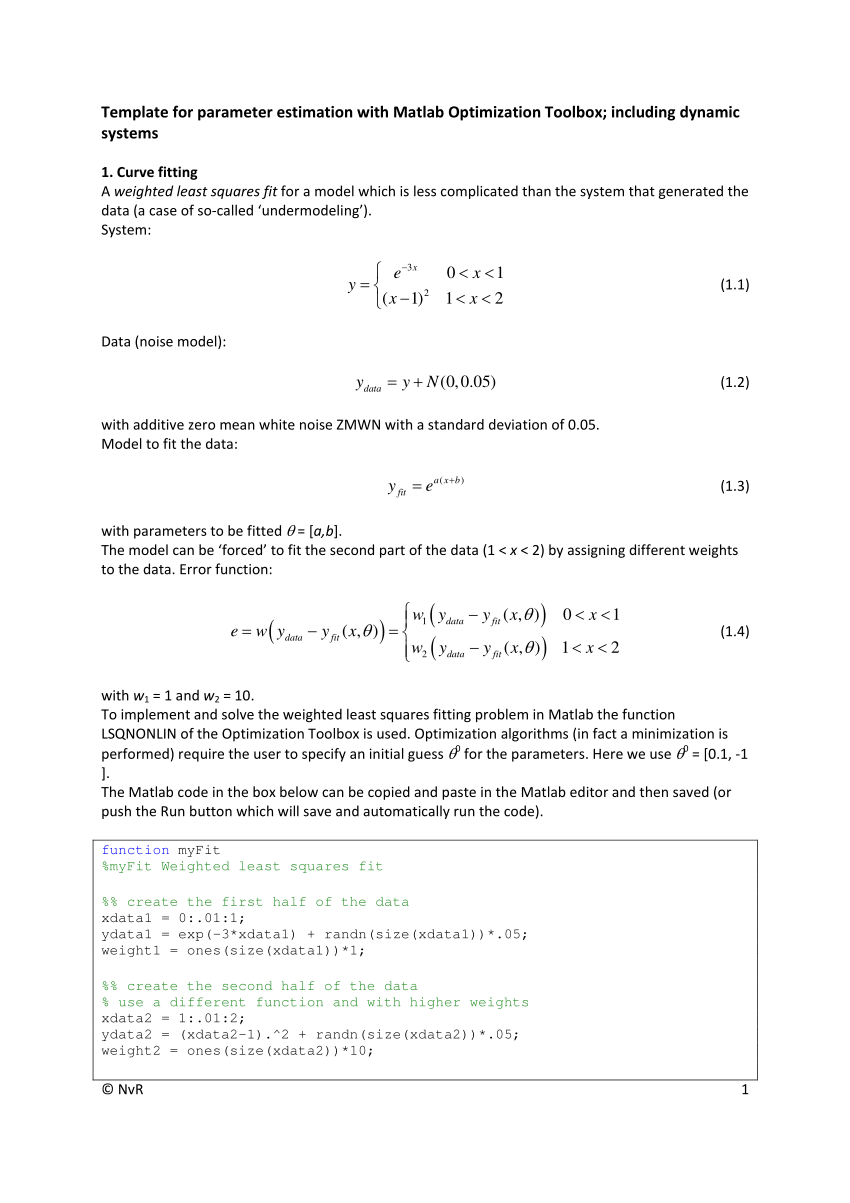
In other contexts the idea of concurrent optimization between process parameters, manufacturing systems and design have been explored using different methodologies. The proposed methodology, known as conditional design optimization (CoDeO), is limited to a NNS manufacturing chain: where, a NNS chain is composed of a primary shaping process and a limited number of machining steps. Quantify benefits by implement it on a case study minimizing turning force) through systematic variation of product design and manufacturing process parameters. The main aim of the NNS optimization approach proposed here is to minimize cost (or time) and improve technological performances (e.g. In contrast, this paper presents a “offline” methodology for selecting the best configuration of design and process parameters in a NNS supply chain, which integrates both product and process design. However, in industrial enterprises and academic literature, product design and manufacturing process optimization are linked by predominately qualitative “ Design-for-X” methodologies rather than the explicit setting of dimensions and process variables. The determination of optimal, or acceptable near-optimal, solutions by a suitable optimization technique has been recognized as critical but difficult task for researchers and practitioners (Mukherjee and Ray 2006). Optimization of such processes must take a broad view and control both process parameters and design variables in order to minimize the raw material utilization and the time of machining operations. NNS manufacturing is a relative, rather than absolute, propriety of a process chain that minimizes raw material utilization and finishing machining operations (Altan and Allen 1990) in comparison with the alternatives (Marini et al.
MATLAB OPTIMIZATION TOOLBOX MULTIPLE DESIGN VARIABLES DRIVERS
In response to these drivers near net shape (NNS) manufacturing processes have emerged as a powerful tool for achieving such savings. The global desire to reduce energy, material consumption and emissions continuously push companies to adopt manufacturing technologies that reduce wastages and maintain productivity. For the specific case study presented the optimized process resulted in cost savings of 22% (corresponding to equivalent machining time savings) and a 10% component weight reduction. After investigation of CoDeO’s requirements, evolutionary algorithms, in particular Genetic Algorithms, are identified as the most suitable for overall NNS manufacturing chain optimization The CoDeO methodology is tested using an industrial case study that details a process chain composed of casting and machining processes.
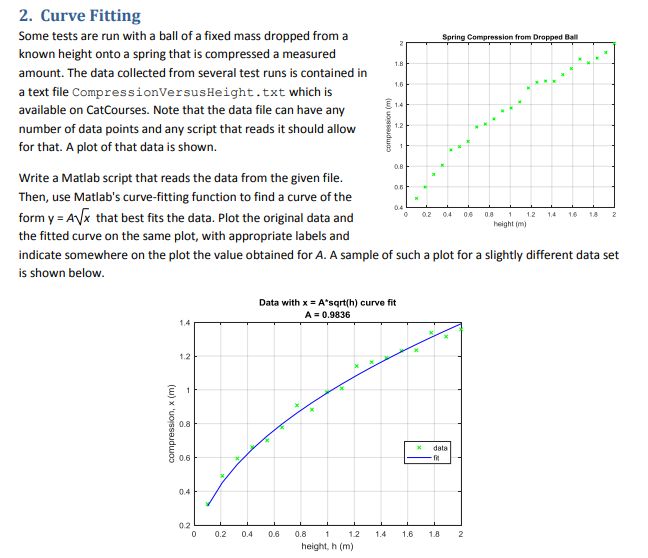
To enable such computation a methodology, named conditional design optimization (CoDeO) is proposed which allows the modelling and simultaneous optimization of process parameters and product design (geometric variables), using single or multi-criteria optimization strategies. In this context the optimisation problem becomes a multi-variable problem in which the aim is to optimize by minimizing cost (or time) and improving technological performances (e.g. The approach assumes a generic manufacturing process in which an initial near net shape (NNS) process is followed by a limited number of finishing operations. This paper presents a new systematic approach to the optimization of both design and manufacturing variables across a multi-step production process.
